News
TAMEST shares news and updates on our membership as well as the latest from the greater Texas research community. Read more about our membership’s recent accomplishments, research breakthroughs and more. Stay up to date by subscribing to the TAMEST digital newsletter. View the past TAMEST newsletters here.
TAMEST New NAS Members Include First Triple Academy Member in Texas
TAMEST congratulates two new members and two current members on their election to the National Academy of Sciences (NAS). Notable among the new elections to the NAS is Lydia E. Kavraki, Ph.D. (NAM, NAE, NAS), of Rice University. With her election to the NAS, she becomes the first TAMEST member to be elected to all three National Academies, a remarkable distinction only 27 other individuals worldwide hold. Margaret Anne Goodell, Ph.D. (NAM, NAS), Baylor College of Medicine, Edith and Peter O’Donnell Awards Committee Chair, who is herself a past recipient of an O’Donnell Award, was also elected to her second academy.
TAMEST Member Profile: Mark Papermaster (NAE), AMD
TAMEST Member Mark Papermaster (NAE) is a visionary technology leader whose four-decade career has helped shape the evolution of modern computing. At AMD, he has been at the helm of the company’s technological transformation, leading the development of its award-winning “Zen” CPU architecture and advancing the capabilities of GPUs and AI-driven computing systems. TAMEST connected with Mr. Papermaster to discuss his role in guiding the future of technology at AMD, the importance of mentorship and what being a member of TAMEST means to him.
TAMEST Members News Roundup – May 2025
From award nominations to media interviews, TAMEST loves to share the accolades of our membership. Read the May compilation of our membership’s recent accomplishments, research breakthroughs and more.
2026 Hill Prizes Applications Now Open
Applications are now open for the 2026 Hill Prizes, funded by Lyda Hill Philanthropies. The prizes propel high-risk, high-reward ideas and innovations that demonstrate significant potential for real-world impact and can lead to new, paradigm-shifting paths in research. The application deadline for the 2026 Hill Prizes is May 31, 2025, at 6 p.m. CT.
Hill Prizes Information Session Slides and Video Available
TAMEST held an Information Session for the 2026 Hill Prizes on Tuesday, April 15, to provide an overview of the prizes, application process and selection criteria. Slides and a video of the session are now available. The Hill Prizes, funded by Lyda Hill Philanthropies, propel high-risk, high-reward ideas and innovations that demonstrate significant potential for real-world impact and can lead to new, paradigm-shifting paths in research. Applications are now open and will be accepted from May 1 – 31, 2025.
O’Donnell Awards Nomination Period Closes April 30
Don’t miss the opportunity to nominate a rising star researcher for the 2026 Edith and Peter O’Donnell Awards before April 30th at 6 p.m. CT. The 2026 Awards will mark 20 years since the awards were first given. The awards recognize rising star Texas researchers who are addressing the essential role that science and technology play in society and whose work meets the highest standards of exemplary professional performance, creativity and resourcefulness.
TAMEST Member Profile: Joan Frances Brennecke, Ph.D. (NAE), The University of Texas at Austin
TAMEST Member and 2025 Hill Prize in Engineering Recipient Joan Frances Brennecke, Ph.D. (NAE), The University of Texas at Austin, is a leading figure in chemical engineering. She is known for her groundbreaking work developing environmentally friendly solvents and processes. TAMEST connected with Dr. Brennecke about her commitment to research and education, her time volunteering for TAMEST and her dedication to mentoring the next generation of engineers.
TAMEST Members News Roundup – April 2025
From award nominations to media interviews, TAMEST loves to share the accolades of our membership. Read the April compilation of our membership’s recent accomplishments, research breakthroughs and more.
TAMEST Welcomes SwRI and Texas Biomed as New Member Institutions
TAMEST is excited to announce the addition of two new member institutions: Southwest Research Institute (SwRI) and Texas Biomedical Research Institute (Texas Biomed). Both are private research institutes located in San Antonio, Texas. TAMEST member institutions are vital partners in fulfilling TAMEST’s mission. Their support enables TAMEST to cultivate and support the next generation of researchers and innovators, increase cooperation across disciplines and address issues critical to the state.
O’Donnell Awards Information Session Slides and Video Now Available
Video and slides from the 2026 Edith and Peter O’Donnell Awards Information Session are now available to learn more about the nomination and selection process for the awards. The 2026 Awards will mark 20 years since the awards were first given. It will be a milestone year to recognize and celebrate the transformative impacts O’Donnell Awards recipients have had on science and society. Nominations are currently open for the 2026 Edith and Peter O’Donnell Awards through April 30th.
TAMEST Profile: Liz Holliday Lerner, TAMEST Director of Communications
Liz Holliday Lerner has been the Director of Communications at TAMEST since 2019. Raised in San Antonio and surrounded by a family immersed in science and research, Liz developed a deep appreciation for science communications from an early age. TAMEST connected with Liz to learn more about her work, passions and how she uses strategic communications, marketing and storytelling to fulfill TAMEST’s mission.
TAMEST Members News Roundup – March 2025
From award nominations to media interviews, TAMEST loves to share the accolades of our membership. Read the March compilation of our membership’s recent accomplishments, research breakthroughs and more.
TAMEST 2025 Annual Conference: Slides and Photos Available
Thank you to all who joined us at the TAMEST 2025 Annual Conference: Transformational Breakthroughs, February 4–6, 2025, at the Westin Irving Convention Center at Las Colinas in Irving, Texas. Speaker slides and photos are now available from the conference sessions. Video from the 2025 Edith and Peter O’Donnell Awards Ceremony is also available. We’re pleased to share some highlights of the meeting with you.
TAMEST Profile: Protégé Poster Challenge Grand Prize Winner Teja Guda, Ph.D., The University of Texas at San Antonio
Earlier this month, Teja Guda, Ph.D., The University of Texas at San Antonio (UTSA), won the Grand Prize at the TAMEST 2025 Annual Conference Poster Challenge. Dr. Guda was one of 43 TAMEST Protégés to participate in the annual TAMEST Protégé Poster Challenge, presented by Shell, and was one of four contest finalists invited to present their poster on stage at the conference. Dr. Guda’s research focuses on developing regenerative strategies and engineering tools for tissue engineering, specifically for musculoskeletal tissue substitutes.
TAMEST Members News Roundup – February 2025
From award nominations to media interviews, TAMEST loves to share the accolades of our membership. Read the February compilation of our membership’s recent accomplishments, research breakthroughs and more.
TAMEST Congratulates 14 Texans Elected to The National Academy of Engineering in 2025
TAMEST welcomes 11 new members and congratulates three current members on their election to the National Academy of Engineering (NAE) in 2025. Of the 14 new members from Texas, three are current members, four are past TAMEST Protégés, two are past conference co-chairs and two are past speakers at a TAMEST annual conference.
TAMEST Board of Directors Appoints New Leadership
The TAMEST Board of Directors is proud to announce the appointment of Ganesh Thakur, Ph.D. (NAE), University of Houston, as Board President and Cheryl Lyn Walker, Ph.D. (NAM), Baylor College of Medicine, as Board Vice President. Both will serve a two-year term beginning February 4, 2025. The TAMEST Board President and Vice President help coordinate and guide the TAMEST Board of Directors in planning strategy, programs and communications.
TAMEST Welcomes 2025 Protégé Class
TAMEST is pleased to welcome 60 talented early-career researchers to the TAMEST 2025 Annual Conference: Transformational Breakthroughs as TAMEST protégés. Each year, TAMEST members have a unique opportunity to help nurture the next generation of researchers in Texas. Through the TAMEST Protégé Program, early-career researchers are selected on an individual basis by TAMEST members to attend the TAMEST annual conference. They also have the opportunity to participate in the TAMEST Protégé Poster Challenge, which recognizes research and technology that could have significant impact on scientific understanding and society.
TAMEST Members News Roundup – January 2025
From award nominations to media interviews, TAMEST loves to share the accolades of our membership. Read the January compilation of our membership’s recent accomplishments, research breakthroughs and more.
Recipients of the 2025 Hill Prizes Announced
TAMEST and Lyda Hill Philanthropies announce the recipients of the 2025 Hill Prizes. The prizes, funded by Lyda Hill Philanthropies, propel high-risk, high-reward ideas and innovations that demonstrate very significant potential for real-world impact and can lead to new, paradigm-shifting paths in research.
TAMEST Names Gerta Hoxhaj, Ph.D., UT Southwestern Medical Center, Recipient of the 2025 Mary Beth Maddox Award and Lectureship
TAMEST has announced Gerta Hoxhaj, Ph.D., Assistant Professor at the Children’s Medical Center Research Institute at UT Southwestern (CRI), as the recipient of the 2025 Mary Beth Maddox Award and Lectureship in cancer research. She was chosen for her work in cancer metabolism and revealing new mechanisms crucial for the growth and survival of cancer cells. Dr. Hoxhaj has opened new channels of understanding in cancer metabolism.
2025 TAMEST Edith and Peter O’Donnell Awards Recipients Announced
The Edith and Peter O’Donnell Awards annually recognize rising Texas researchers who are addressing the essential role that science and technology play in society, and whose work meets the highest standards of exemplary professional performance, creativity and resourcefulness. Learn more about the 2025 Edith and Peter O’Donnell Awards recipients.
TAMEST Member Profile: John L. Junkins, Ph.D. (NAE), Texas A&M University
TAMEST Member John L. Junkins, Ph.D. (NAE), Texas A&M University, is a pioneering aerospace engineer who has spent more than five decades shaping the future of his field while mentoring the next generation of researchers and innovators in our country. TAMEST connected with Dr. Junkins to learn more about his remarkable career path, expanding the number of National Academy members in Texas thanks to The Hagler Institute at Texas A&M and more.
TAMEST Members News Roundup – December 2024
From award nominations to media interviews, TAMEST loves to share the accolades of our membership. Read the December compilation of our membership’s recent accomplishments, research breakthroughs and more.
TAMEST Recognizes Lyda Hill and Lyda Hill Philanthropies with Kay Bailey Hutchison Distinguished Service Award
TAMEST is pleased to announce Lyda Hill and Lyda Hill Philanthropies as the recipients of the Kay Bailey Hutchison Distinguished Service Award. TAMEST is recognizing Lyda Hill and her team for empowering and enabling groundbreaking research in science and nature that profoundly impacts society.
TAMEST Member Bob Metcalfe, Ph.D. (NAE) Makes Generous Donation to Support National Academies Advancement
TAMEST is proud to announce a generous gift of $25,000 from renowned innovator, co-inventor of Ethernet and internet pioneer Bob Metcalfe, Ph.D. (NAE), The University of Texas at Austin, to support our National Academies Advancement Initiative. Dr. Metcalfe’s contribution is a major endorsement of TAMEST’s efforts to advance the next generation of trailblazing researchers.
TAMEST Member Profile: Sharon Y.R. Dent, Ph.D. (NAS), MD Anderson Cancer Center
TAMEST Member Sharon Y.R. Dent, Ph.D. (NAS), The University of Texas MD Anderson Cancer Center, is a global leader in chromatin research and her foundational work has helped define the role of chromatin in both normal developmental processes and disease states. TAMEST connected with Dr. Dent to learn more about her long and successful commitment to education, research and mentoring.
TAMEST Members News Roundup – November 2024
From award nominations to media interviews, TAMEST loves to share the accolades of our membership. Read the November compilation of our membership’s recent accomplishments, research breakthroughs and more.
TAMEST Welcomes Six Texans Elected to the National Academy of Medicine (NAM)
TAMEST congratulates five new members and one current member on their election to the National Academy of Medicine (NAM). The six elected include a current TAMEST member and former Edith and Peter O’Donnell Award recipient, two former TAMEST protégés as well as the first member to be elected from Texas Southern University. TAMEST will welcome these and other new Texas-based National Academy members at the opening reception of the TAMEST 2025 Annual Conference on February 4, 2025, in Irving, Texas.
TAMEST Member Elaine Oran, Ph.D. (NAE, FREng), Texas A&M University, Elected to the Royal Academy of Engineering
TAMEST congratulates TAMEST Member Elaine Oran, Ph.D. (NAE, FREng), Texas A&M University, on her election to the Royal Academy of Engineering (FREng). Dr. Oran is an expert on numerical methods for large-scale simulation of physical systems. She was first elected to the National Academy of Engineering (NAE) in 2003 for unifying engineering, scientific and mathematical disciplines into a computational methodology to solve challenging aerospace combustion problems.
TAMEST Profile: Ralph DeBerardinis, M.D., Ph.D. (NAM), UT Southwestern Medical Center
TAMEST Member and Mary Beth Maddox Award and Lectureship Committee Chair Ralph DeBerardinis, M.D., Ph.D. (NAM), UT Southwestern Medical Center, is a world-renowned expert in metabolism. In 2019, he received the Edith and Peter O’Donnell Award in Medicine and in 2020, he was elected to the National Academy of Medicine for his work in cancer metabolism, which has changed our understanding of how tumors reprogram metabolic pathways to maximize energy production and growth. TAMEST connected with Dr. DeBerardinis to learn more about his research, leadership at TAMEST and the importance of recognizing cancer researchers in Texas.
TAMEST Members News Roundup – October 2024
From award nominations to media interviews, TAMEST loves to share the accolades of our membership. Read the October compilation of our membership’s recent accomplishments, research breakthroughs and more.
TAMEST Celebrates 20 Years of Innovation and Impact at Pegasus Park
On Tuesday, September 3, TAMEST gathered more than 70 National Academy members, research institution leaders and others from the research community to attend a special 20th Anniversary Reception and networking event at Pegasus Park in Dallas. The evening featured an on-stage conversation with Former United States Senator The Honorable Kay Bailey Hutchison, who co-founded TAMEST in 2004, TAMEST Board President Brendan Lee, M.D., Ph.D. (NAM), Baylor College of Medicine and UT Southwestern Medical Center President and TAMEST Member Daniel K. Podolsky, M.D. (NAM). The program showcased TAMEST’s history and growth over the past 20 years and its potential in the future.
Registration is Now Open for TAMEST 2025 Annual Conference
Registration is now open for the TAMEST 2025 Annual Conference: Transformational Breakthroughs, February 4–6, 2025, at the Westin Irving Convention Center at Las Colinas in Irving, Texas. The conference will explore some of the most disruptive breakthroughs in science and technology set to change our way of life in the coming years. Speakers will examine game-changing advancements in the fields of materials science and nanotechnology, space exploration, regeneration and synthetic biology, energy transition and more. Register early to save 25% on registration through Thursday, November 21, 2024.
Mary Beth Maddox Award Nomination Deadline Ends on September 30
There is still time to nominate for the 2025 Mary Beth Maddox Award and Lectureship. Don’t miss this opportunity to recognize a woman scientist in Texas bringing new ideas and innovations to the fight against cancer. In addition to being honored at the TAMEST 2025 Annual Conference with a $5,000 honorarium and presentation, the recipient will promote their work and discoveries across the state at established lecture and seminar series at TAMEST member institutions with NIH National Cancer Institute Designated Cancer Centers.
TAMEST Profile: Vanessa Wyche (NAE), Director, NASA’s Johnson Space Center
TAMEST Member Vanessa E. Wyche (NAE) is the Director of NASA’s Johnson Space Center, where she oversees more than 11,000 civil servants and contract employees, all dedicated to advancing human spaceflight. TAMEST spoke with Director Wyche to gain insight into her extraordinary career and her vision for NASA’s future private and public partnerships and to learn more about her dedication to promoting STEM education and mentoring the next generation of engineers.
TAMEST Members News Roundup – September 2024
From award nominations to media interviews, TAMEST loves to share the accolades of our membership. Read the September compilation of our membership’s recent accomplishments, research breakthroughs and more.
Zhijian “James” Chen, Ph.D., Awarded the Albert Lasker Basic Medical Research Award
TAMEST Member and 2007 O’Donnell Award in Biological Sciences Recipient Zhijian “James” Chen, Ph.D. (NAM, NAS), UT Southwestern Medical Center, has been awarded the Albert Lasker Basic Medical Research Award for his discovery of the cGAS enzyme, which senses invading pathogens and triggers the body’s innate immune system. The Lasker Awards, often called “America’s Nobels,” recognize significant advances in the understanding, diagnosis, treatment, cure, and prevention of human disease and are regarded as the country’s preeminent biomedical research prize.
TAMEST to Hold 20th Anniversary Reception Next Week in Dallas
Next week, TAMEST will gather its members, research institution leaders and others from the research community in the region to attend a special 20th Anniversary Reception and networking event at Pegasus Park in Dallas. The event will take place on Tuesday, September 3, from 5–7:30 p.m. The evening will feature an on-stage conversation with Former United States Senator The Honorable Kay Bailey Hutchison, TAMEST Board President Brendan Lee, M.D., Ph.D. (NAM), Baylor College of Medicine and UT Southwestern Medical Center President Daniel K. Podolsky, M.D. (NAM), commemorating the 20th anniversary of TAMEST.
2025 Mary Beth Maddox Award and Lectureship Nominations Now Open
Nominations are now open for the 2025 Mary Beth Maddox Award and Lectureship. Don’t miss this opportunity to nominate a woman scientist in Texas bringing new ideas and innovations to the fight against cancer. The nomination deadline for the 2025 Mary Beth Maddox Award and Lectureship is Monday, September 30, 2024, at 6 p.m. CT.
TAMEST Profile: Walter E. Voit, Ph.D., UT Dallas
TAMEST 2025 Annual Conference Science Co-Chair Walter E. Voit, Ph.D.’s innovative work at the cross-section of engineering, materials science, artificial intelligence, computer engineering and polymer science has propelled him to significant developments in 3D printing and digital immersive innovation across academia and industry. TAMEST connected with Dr. Voit to learn more about his work, the importance of cross-discipline research and the TAMEST 2025 Annual Conference.
TAMEST Members News Roundup – August 2024
From award nominations to media interviews, TAMEST loves to share the accolades of our membership. Read the August compilation of our membership’s recent accomplishments, research breakthroughs and more.
2025 Mary Beth Maddox Award and Lectureship Nominations Open August 1
Nominations for the 2025 Mary Beth Maddox Award and Lectureship will open August 1 through September 30, 2024. The award recognizes women scientists in Texas bringing new ideas and innovations to the fight against cancer. The recipient will be recognized with a $5,000 honorarium and award and present their research at the TAMEST 2025 Annual Conference: Transformational Breakthroughs, February 4–6, 2025, at the Westin Irving Las Colinas in Irving, Texas.
Final Lecture with 2023 MBM Awardee at UT Southwestern Medical Center
2023 Mary Beth Maddox Award and Lectureship Recipient Florencia McAllister, M.D., MD Anderson Cancer Center, presented her groundbreaking research on May 22, 2024, to more than 60 individuals as part of the Mary Beth Maddox Lecture Series. The lecture was part of UT Southwestern Medical Center’s Excellence in Immunology Seminar Series (in partnership with Simmons Cancer Center).
TAMEST Profile: Aaron T. Becker, Ph.D., University of Houston, TAMEST 2024 Protégé Poster Challenge Winner
This February, roboticist Aaron T. Becker, Ph.D., University of Houston (UH), was one of 42 TAMEST Protégés to participate in the annual TAMEST Protégé Poster Challenge, sponsored by Shell Global Solutions US. Dr. Becker was awarded first prize for his poster presentation, Magnetic Milli-scale Robots for Blood Clot Removal. TAMEST connected with Dr. Becker to learn more about his swarm robotics research and experience participating in TAMEST’s protégé program.
TAMEST Members News Roundup – July 2024
From award nominations to media interviews, TAMEST loves to share the accolades of our membership. Read the July compilation of our membership’s recent accomplishments, research breakthroughs and more.
TAMEST Welcomes Six Texans Elected to the National Academy of Sciences in 2024
TAMEST is proud to welcome five new members and one current member elected to the National Academy of Sciences (NAS) in 2024. The six were among the 120 members and 24 international members elected in recognition of their distinguished and continuing achievements in original research.
TAMEST Staff Profile: Destiny Allen, TAMEST Program Officer
TAMEST’s newest addition to the staff, Destiny Allen, recently moved from Arizona where she attended Arizona State University and received an M.S. in Sustainable Development and Technology. She has extensive experience in the nonprofit sector and has worked with the Peace Corps in West Africa as well as the Sierra Club in Columbus, Ohio. TAMEST connected with Destiny to learn more about her work for TAMEST and why she’s passionate about working on programs such as the Mary Beth Maddox Award and Lectureship and the importance of mentorship for individual success.
2025 Hill Prizes Applications Now Open
Applications are now open for the 2025 Hill Prizes, funded by Lyda Hill Philanthropies. The prizes propel high-risk, high-reward ideas and innovations that demonstrate very significant potential for real-world impact and can lead to new, paradigm-shifting paths in research. The application deadline for the 2025 Hill Prizes is May 31, 2024.
TAMEST Members News Roundup – May 2024
From award nominations to media interviews, TAMEST loves to share the accolades of our membership. Read the May compilation of our membership’s recent accomplishments, research breakthroughs and more.
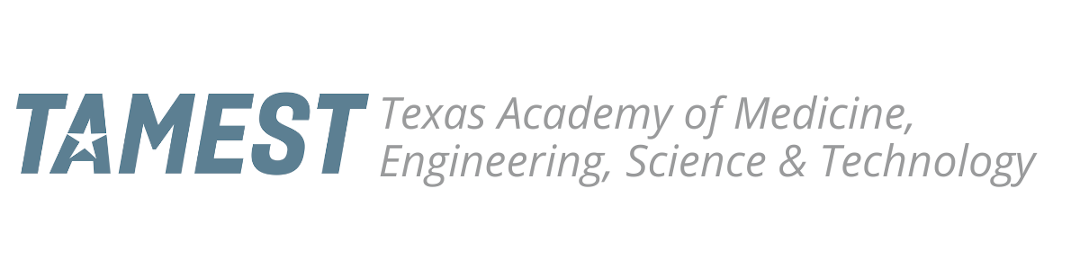