Q&A with Dr. Joseph Beaman: 3-D Printing Pioneer
Dr. Joseph J. Beaman is the Earnest F. Gloyna Regents Chair in Engineering in the Department of Mechanical Engineering at The University of Texas at Austin and was elected to the National Academy of Engineering (NAE) in February 2013. He was elected to the NAE for innovation, development, and commercialization of solid freeform fabrication and selective laser sintering, an early form of additive layer manufacturing also known as 3-D printing—one of the most popular topics in the tech space currently.
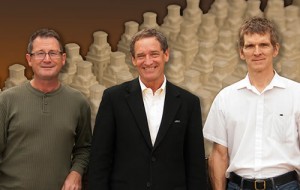
From left to right: Carl Deckard, Joe Beaman, and Paul Forderhase photographed on November 19, 2012. The image in the background is of selective laser sintered miniature UT Austin towers before removal from the powder bed.
Dr. Beaman coined the term Solid Freeform Fabrication in 1987 referring to a manufacturing technology that produces freeform solid objects directly from a computer model of the object without part-specific tooling or knowledge. He was the first academic researcher in the field beginning in 1985, and one of the most successful Solid Freeform Fabrication approaches, Selective Laser Sintering (SLS), was developed in his laboratory at UT Austin. Carl Deckard, a student working in Dr. Beaman’s lab, came up with the idea as an undergraduate and pursued it further while working on his master’s degree. He and Dr. Beaman, who was the Principal Investigator (PI), received a $30,000 grant from the National Science Foundation (NSF) to advance the technology and build a proof of concept machine.
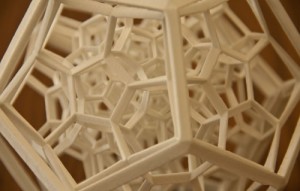
This is an example of a complex selective laser sintered object. All of the interior objects were manufactured at one time from a tough nylon polymer on a SinterStation 2000 machine.
Dr. Beaman worked with graduate students, faculty, and industrial suppliers on the fundamental technology including materials, laser scanning techniques, thermal control, mold- making techniques, direct metal fabrication, and biomedical applications. He was one of the founders of DTM Corporation (later acquired by 3-D Systems), that commercialized SLS technology. Dr. Beaman was in charge of advanced development for DTM during 1990–1992 when the company developed and marketed its first commercial systems.
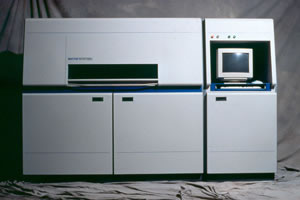
The SinterStation 2000
Today, Dr. Beaman is considered a pioneer in what is popularly known as 3-D printing. His work with SLS-based technology is used by manufacturers globally to dramatically compress the manufacturing cycle for complex parts. Benefits include greatly reduced cost, time, and the capability to achieve in a single operation, geometries that would otherwise require multiple operations or prove impossible to manufacture with standard techniques. The technology is broadly applicable to many fields including architecture, industrial design, automotive and aerospace engineering, military applications, medicine/healthcare, civil engineering, fashion, and food.
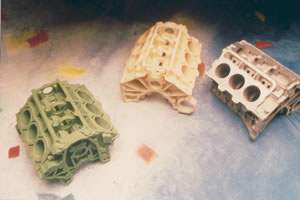
SLS was originally intended by Deckard as a way to make wax models for a casting process known as investment casting or lost-wax casting. The part made of green wax (left) can be used as a casting pattern to make an identical part out of aluminum (right) or other metal. The off-white part (center) is made of polycarbonate and is not involved in the investment casting process.
According to Wohlers Associates, a leading 3-D printing consultancy, the market for 3-D printing and additive manufacturing in 2012, consisting of all products and services worldwide, grew 28.6% (CAGR) to $2.204 billion. By 2017, Wohlers Associates believes the sale of 3-D printing products and services will approach $6 billion worldwide. And its adoption continues to expand among consumers and professionals with a wide range of price points and capabilities aligned with the needs of each group. UPS is testing the market for 3-D printing services in stores in San Diego and Washington D.C. Approximately 80 percent of 3-D printing customers in the San Diego store were medical students interested in prototypes. NASA recently tested a rocket with a 3-D printed fuel injector. 3-D printing technology allowed the part to be created in just two parts instead of 115. NASA is also working with the company Made in Space and plans to launch a new 3-D printer in June 2014 for use on the International Space Station.
To provide more insights on the origins of SLS and the future of 3-D printing, we caught up with Dr. Beaman. He was kind enough to participate in the following Q&A.
When you and Carl Deckard began work in the mid-1980s on Selective Laser Sintering (SLS) what were you envisioning as the major industries and primary applications for commercial use of this technology?
Dr. Beaman: When Carl and I first discussed the concept, we were most concerned about how long it took to make the first one of almost anything. Carl’s interest was in parts that might come out of a standard machine shop, and I had worked in a machine shop while in high school, so I am sure this background colored our thoughts. Of course machine shops support many different types of industries that make mechanical parts.
What were the major challenges you and your team faced in the early days of DTM Corporation in developing SLS machines for use in commercial engineering/manufacturing environments?
Dr. Beaman: By its nature, SLS can make a wide variety of different shapes and therefore can be used in a numerous applications. This is a blessing and a curse. There are many possible markets, but a small company cannot address them all, especially when the market has to be created. Deciding what to focus on was the biggest challenge. We decided on casting and prototyping as a start. By the way, we also looked at an inexpensive SLS machine, which Paul Forderhase briefly studied. Paul was a master’s student that built the second SLS machine at UT and later joined DTM.
The core SLS patents will expire in February 2014. There’s speculation this could allow Chinese manufacturers to enter the market and effectively lower the prices for quality 3-D printers leading to the development of desktop SLS devices. What are your thoughts about the potential impact of these patents expiring?
Dr. Beaman: This is possible, but there are other specific patents that have longer life in this area and some of these may preclude a wholesale entrance by Chinese manufacturers in the general market.
3-D printing seems to be exploding in popularity with both consumers and industry with new applications being developed at a rapid pace. Many of these applications were not even imagined by the inventors of the technology. Where do you see the industry headed now almost 30 years since its inception?
Dr. Beaman: We have always split the market based on two axes, accuracy and strength. I usually refer to low accuracy and low strength applications as “3-D Printing.” This is the consumer market that includes a growing number of consumer-focused products from companies such as Makerbot, etc. This is the market that has exploded. Sometimes the market confuses the capabilities of 3-D Printers with higher performance additive manufacturing machines.
High strength, low accuracy yields machining forms. In which low accuracy “machining forms” are produced for final machining. Aerojet was a company that was formed to address this market for titanium (Ti) machining forms but went out of business because of competition with numerical control (NC) machining.
High accuracy, low strength yields casting patterns, which is a viable market. This includes patterns for lost-wax casting processes or for foundry casting patterns or molds. Applications here include jewelry, medical instruments and devices, and mechanical parts or forming operations.
Moderate accuracy, moderate strength is the realm of rapid prototyping. Rapid prototyping is a strength for our SLS technology and has applications in a wide range of manufacturing industries.
The Holy Grail is high strength, high accuracy, which is true manufacturing. I see true additive manufacturing as a strong direction now especially as an educated workforce gets developed that understands the design freedom allowed by additive manufacturing. This educated workforce will happen because of the 3-D printing market.
Are there new technologies under development that will further expand 3-D printing capabilities for both consumers and industrial design and manufacturing applications?
Dr. Beaman: A third axis is multiple materials. This would allow fabrication of system components such as parts with physically embedded electronics or structures with graded or discrete material interfaces. This will require improvements in CAD solid modeling software.
Will there continue to be market segmentation between complex industrial applications versus consumer applications for 3D printing or will this division begin to diminish as the technology evolves?
Dr. Beaman: For now, I see continued market segmentation unless someone comes up with a very inexpensive additive manufacturing machine that has great mechanical properties and accuracy.
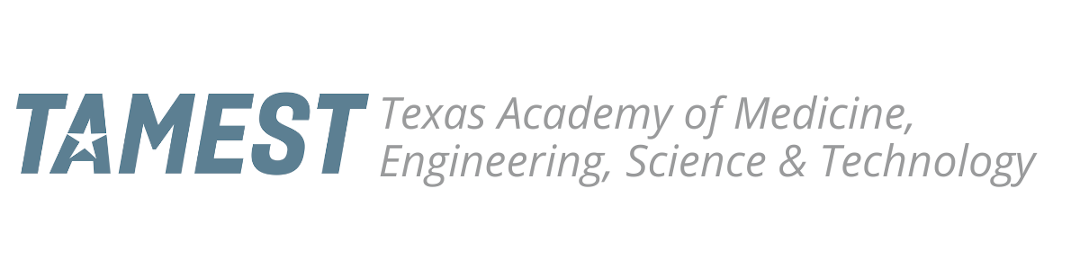